在庫管理の基本は発注!~4つの発注方法を詳しく解説~
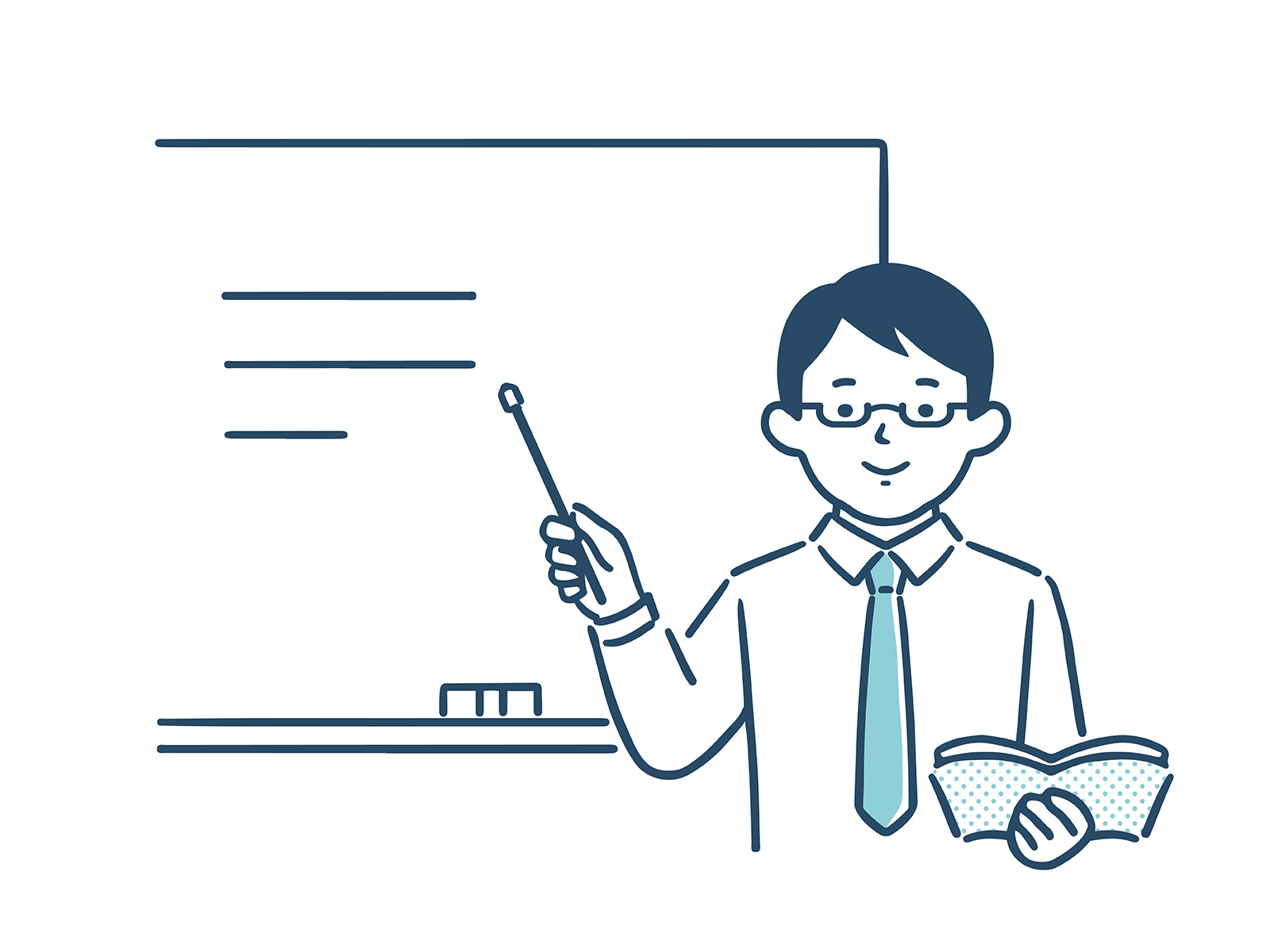
在庫管理の基本は発注!~4つの発注方法を詳しく解説~
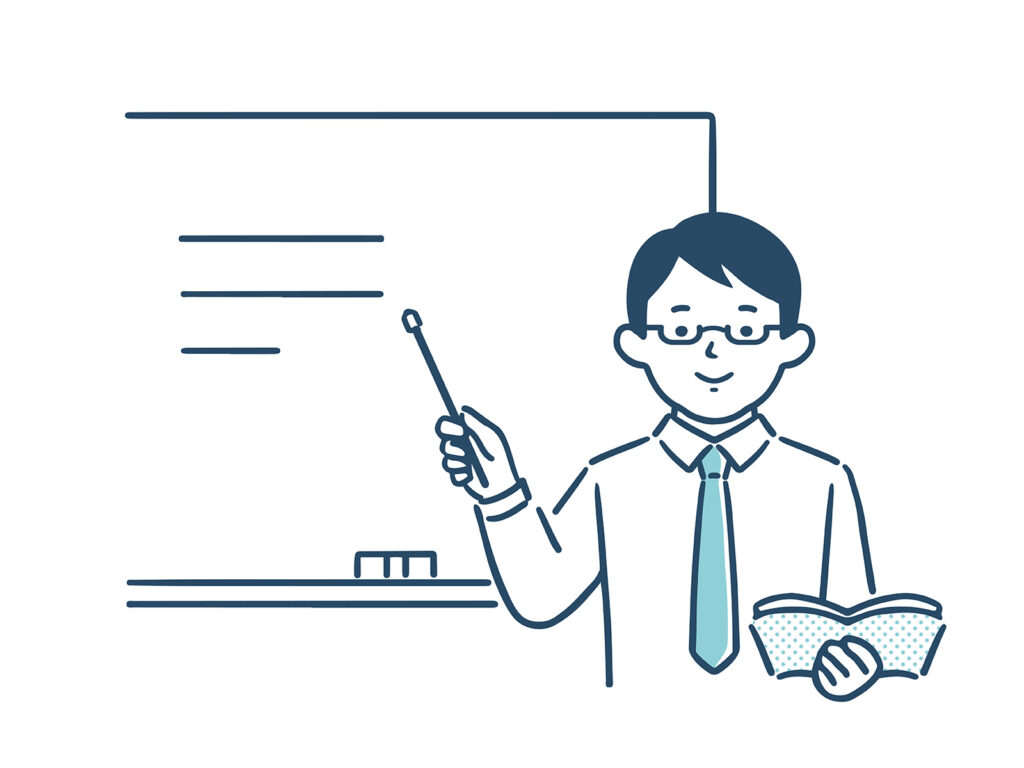
発注コントロールは在庫量最適化の一番の近道
在庫管理は手元にある在庫の量を適正な水準に維持することです。「出」はコントロールできないので、「入」をコントロールするしかありません。すなわち在庫管理の技術とは、発注の技術なのです。
在庫管理を行うということは、需要に合わせて正しく発注するということです。制約条件に応じて採用すべき発注法について解説します。
自ら余剰在庫を意識し、在庫消化を促進させる
ツールをお探しでは
ありませんか?
・定価で販売できる商品を値引きしていないか
・アナログ作業による在庫管理で業務負担が大きくなっていないか
・値引きやクーポンの判断が担当者の勘や慣例頼みになっていないか
企業のEC運用担当者が継続的に、より簡単に「余剰在庫の最小化」の工夫を行うことができ、CV(コンバージョン)や目先の短期的な売上、値引きの施策のみに頼らない粗利最大化の支援を行うことができます。さらにCRMシステム「LTV-Lab」との連携により売れない理由を究明し、アクションにつなげます。是非詳しい機能や特徴をサービスページからご覧ください。
4つの発注法とは
在庫管理を行うということは、具体的には、「補充(発注)を管理する」ということになります。
出荷は取引先から受ける注文によって決まるので、自ら管理することは不可能です。
ですから、出荷の状況に合わせて、必要な時期に必要な量の補充を行うのです。
このために必要なのが発注の技術、すなわち発注法です。
発注法といえば、一般的に「4つの発注法」が知られており、それは以下のようなものです。
発注するタイミングが定期的かどうか、発注する量が決まっているかどうかという2つの要素から、4つに区分されているのだということがわかるでしょう。
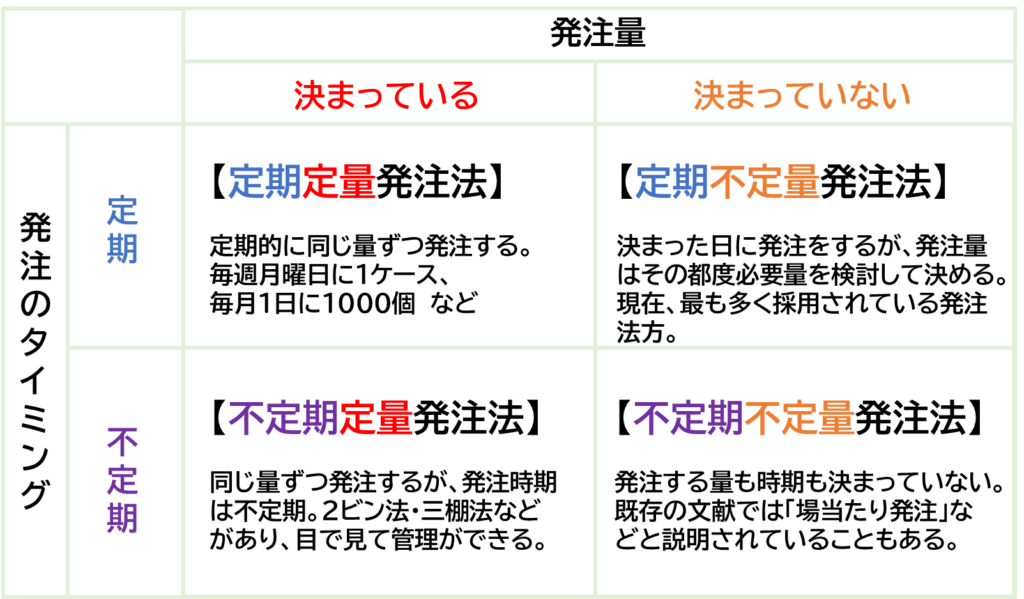
①定期定量発注法
定期定量発注法については、 まず考える必要がないといえます。
需要が変動するために在庫管理が必要になっているのに、「定期的」に「定量」を発注することを続けていれば、必ず欠品か在庫過剰かにつながってしまうからです。
②不定期定量発注法
不定期定量発注法はデータを使わずに在庫管理ができる手法です。
お勧めの方法というわけではありませんが、活用できる場合もあるのでここで紹介しておきます。
ただし簡便な分、在庫が過剰になっていても気がつきにくいという欠点があります。
データの不要な不定期定量発注法 (2ビン法・三棚法)
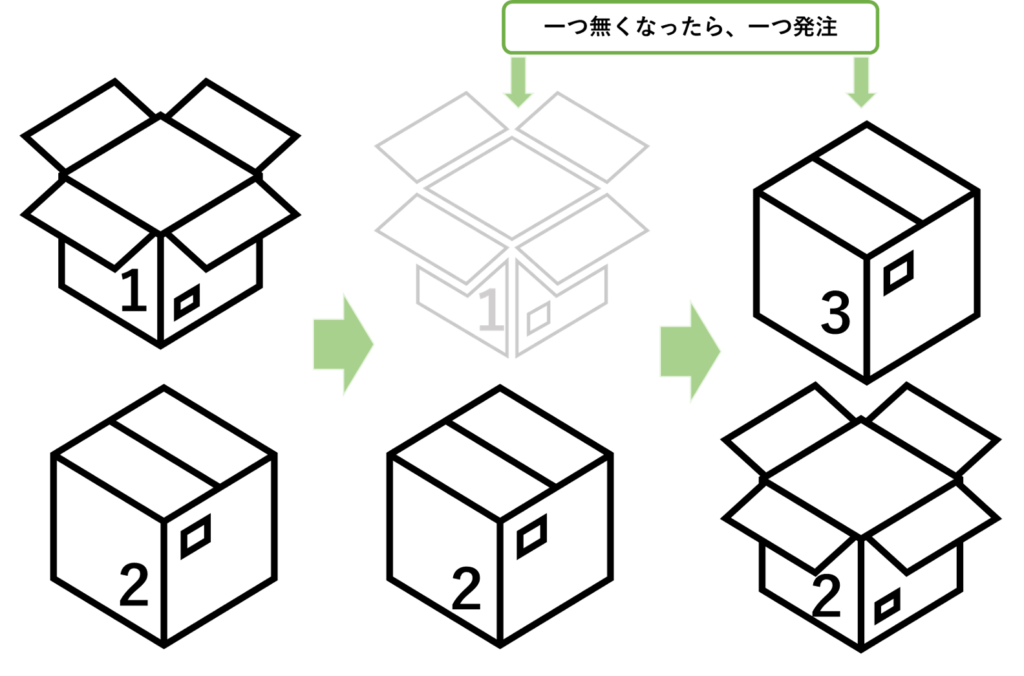
2ビン法を例にとって、不定期定量発注法を説明しましょう。
ビンとはbin、英語で「容器・入れ物」の意味と考えるとわかりやすいようです。
2つの同じ入れ物 を用意して在庫し、1つが空になれば1つ補充 (発注) するというものです。
空になったタイミングで発注するから「不定期」、ビンのサイズは変わらないから「定量」ということです。
出荷状況や在庫状況についてデータを収集・分析せずとも、”適当な”発注がで きる仕組みなのです。
コンピュータがなくても、ベテランの担当者がいなくても 一定レベルの管理ができるというわけです。
三棚法もほぼ同様の仕組みで、3つの棚を用意して1つ空いたら1つ補充するというものです。
「目で見て管理できる」 という点は非常に簡便で高く評価したいところですが、一方、この方法には大きな弱点があります。
管理レベルが入れ物の大きさに制約されてしまうということです。
たとえば、初めに2ケースを用意して、1ケースなくなったら1ケース補充するとしている場合、この「1ケース」というのが何日分 にあたるのか、誰も知らないまま管理が行われることになるのです。
需要が変動するために在庫管理が必要とされているのだという立場から見れば、ある程度の有効性は認められるものの、在庫管理の手法としては低いレベルのものといわざるを得ません。
欠品や過剰に気づきにくい不定期定量発注法
イメージがわきやすいように、 数字を入れて説明してみましょう。
ここに100個入りのケースがあったとします。 1つのビンが空になれば、1ケースつまり100個の補充がなされます。
その商品が1ヶ月に1個しか売れない商品でも、100個補充されてしまうのです。
もし、そのままの売れ行きが続くとしたら、100個は100ヶ月分に相当します。約8年分ということです。
こんなに在庫しておきたい人はどこにもいないでしょう。
しかし、この手法をとっている限り、こんなことは日常茶飯事で起こり得ます。
しかも、8年分もの大量の在庫を一気に補充してしまったことに気がつく人すらいません。
出荷状況、 在庫状況をデータで見ることがないからです。
皮肉に聞こえるかもしれませんが、データを見ないで管理しようとするがゆえに、そんなことも起こってしまうのです。
では、欠品は起こらないように管理できるかといえば、そうでもありません。
リードタイムの長い商品を、出荷動向に関係なく1ケースしか持っていなければ、出荷が立て続けに発生して欠品するということも、当然起こるでしょう。
欠品は、過剰在庫よりも発見しやすいので、傷が浅くてすむかもしれないという程度です。
不定期定量発注法では欠品や過剰が起こりやすく、しかも、その状態になかなか気づくことができません。
この方法をあまりお勧めしない理由は、まさにそこにあります。
適用するとしても、在庫品のすべてをこの方法で管理することは、危険なことといわざるを得ません。
この発注法に限らず、どんなに綿密に在庫管理を行っても、100%欠品をなくすことはまず不可能です。
だとすれば、何か問題が起こったときに迅速に的確な行動がとれる仕組みを備えておきたいものです。
その意味でも、不定期定量発注法では、正しいデータがとれないため、安心できる仕組みとはいい難いのです。
不定期定量発注法を適用できるのは、日々の在庫量をコンピュータに登録するような手間を省きたい商品や、多少過剰在庫になっても構わないような、原価の安い商品に限られるといえるでしょう。
総括すれば、この手法は、在庫状況、出荷状況を分析した上で発注業務を行うということが煩雑であるがゆえに、考え出された苦肉の策であるということができます。
コンピュータを利用することにより、毎日の需要の変動を追いかけることが容易になれば、ビンの大きさに悩まされることもありません。
つねに需要に合わせた在庫量を算出し、これを維持することが可能になるわけです。
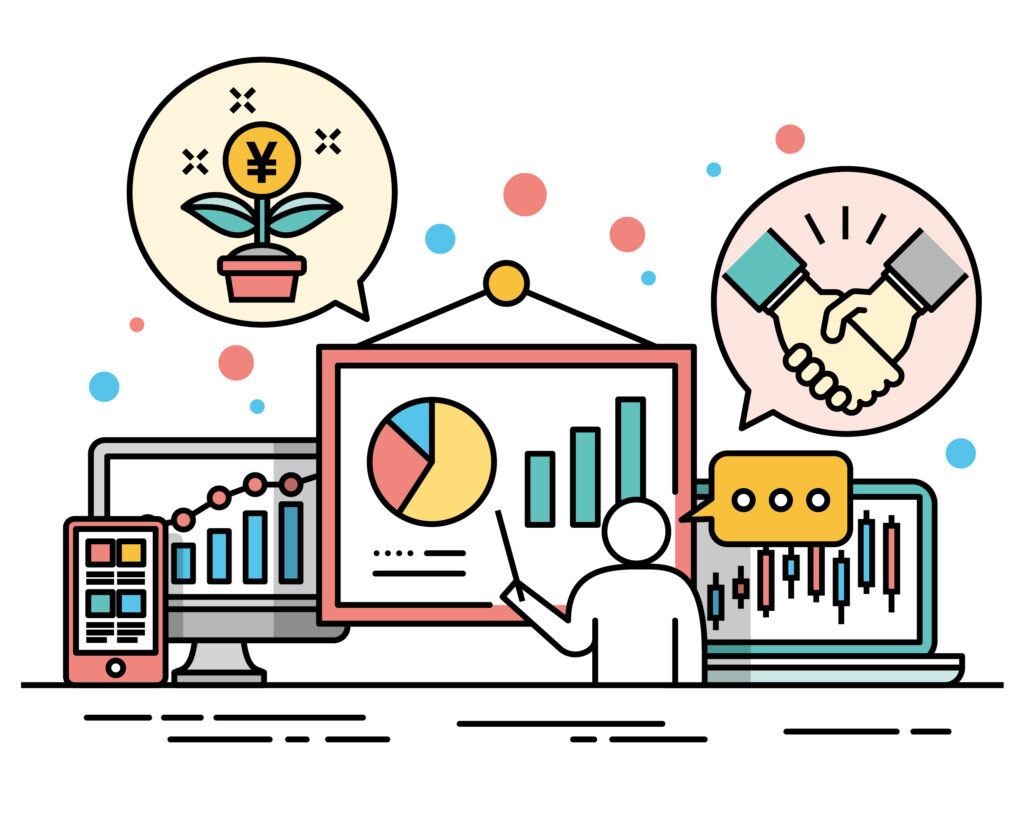
③定期不定量発注法
おそらく日本で一番普及している発注法です。生産サイクルのあるメーカー、発注タイミングが決まっている流通業者などは、 この方法を採用することになります。
発注時期に制約があるなら、この方法をとる
定期不定量発注法は、 発注時期に制約がある場合にとられる発注法です。
「発注時期に制約がある」とは、どういう場合かを見てみましょう。
以下はすべて発注時期に制約があるといえる状況です。
● 週単位、旬単位、月単位などの生産サイクルにしたがって生産するメーカーである
●調達は「○日ごと」、「○曜日」など、タイミングが決まっている
●発注はいつでもできるが、それに応じて納品してもらえるタイミングは「○曜日」など、決まっている
「○日ごと」、「○曜日」のように、定期的に発注する時期が決まっているということから、「定期不定量発注法」と呼ばれるのです。
生産サイクルのないメーカー、 つまり毎日生産計画を立てているようなメーカーはあまりないでしょうから、ほとんどのメーカーは、この方法を採用していると思われます。
流通業者ならば、生産サイクルにこだわらずに発注が可能と思われますが、自社の業務スケジュールにしたがい、発注日や発注曜日を決めているところはあります。
このような場合にも、「定期不定量発注法」が採用されます。
毎日発注するけれども、カテゴリごとに発注可能日が決まっているといった場合にも 「定期不定量発注法」となります。
いつでも発注できる場合は、「不定期不定量発注法」が採用されます。こちらについては次の節で紹介します。
発注時期に制約があるがゆえに 「思惑」が入り込むことも
定期不定量発注法が採用される現場では、急に在庫が減ったからといって発注することは原則としてできません。
このため、発注担当者によっては、過去の実績 から見て必要と思われる以上に発注してしまうことがあります。
欠品を避けたい心情を理解できないわけではありませんが、過剰在庫を抱えてしまうことは会社の損失につながります。
やはり、適正在庫に抑え込むことを目標にすべきです。
定期不定量発注法をとる場合、発注日に検討すべき内容は、次の納品予定日までの出荷量を予測し、現在庫と比べて欠品しそうかどうか。を考えます。
次の納品予定日までの期間をLT(リードタイム)と呼びます。
④不定期不定量発注法
発注時期に制約がないならば、 不定期不定量発注法を採用します。
流通業者のほか、メーカーであっても、地方拠点から工場倉庫への発注であれば採用できる可能性があります。
「必要なものを必要なときに必要なだけ」 発注する
需要が変動するからこそ在庫管理が必要です。定期不定量発注法では先の見通しは完全に読めないことから、担当者の思惑が入り込み、在庫の過剰や絞り込みすぎが問題になる可能性がありました。
不定期不定量発注法では、思惑が入り込む問題はあまり心配いりません。
急に出荷が増えて在庫が減ってしまったら、慌てることなく発注すればよいだけです。
逆に、出荷が減って在庫が余りがちという状況になれば、発注しなければよいのです。
定期不定量発注法に比べて、発注担当者のストレスは少ないといえそうです。
不定期不定量発注法を採用できるのは?
不定期不定量発注法を採用できるのは、流通業者に多いと思われます。
小売業者の卸売業者に対する発注、 卸売業者のメーカーに対する発注などが考えられます。
ただし、「発注はいつでも受け付けてもらえるが納品は週に1回」 などと決まっている場合には、
不定期不定量発注法では対応できません。納品のタイミングが 限定されているならば、そこからリードタイムをさかのぼった日を発注日として考え、定期不定量発注法で運用する必要があります。
メーカーでも不定期不定量発注法を採用できる可能性はあります。
生産サイクルと切り離した管理ができる在庫ならばよいのです。
たとえば、すでに工場倉庫に製品として置かれている在庫です。
注文に応じていつでも出荷できるならば、 不定期不定量発注法を適用できます。
メーカーの社内移動ということになりますが、地方拠点から工場倉庫への補充依頼については、不定期不定量発注法が採用できる可能性が高いと思われます。
発注量を 「1車単位」にまとめることを考慮する
在庫管理では、必要なものを必要な量だけ維持することが至上命題です。
しかし現在、物流危機と言われる状況下で「利用する車両を必要最小限に絞り込む」ことの重要性が増してきています。
今後、車両はますます逼迫することが想定されています。
不定期不定量発注法 を採用した場合に、発注に対応する納入車両が積載率の低い状態になるとしたら、そのまま発注することはせず、発注量が1車単位にまとまるような別ルールを付け足すことも求められます。
推奨されるのは「不定量」 発注法
採用をお勧めしたいのは「不定量」発注方法の2つです。
在庫管理は需要が変動するために行うわけですから、なるべく変化に対応する力が強い方法を採用する必要があります。
そこで、 発注する量を需要の変動に合わせられるよう、 不定量にするべきだと考えるのです。
発注のタイミングについては、定期と不定期があるわけですが、これは発注時期に制約があるかどうかで選択することになります。
何も制約がないならば、不定期を選択します。
しかし、メーカーにおいて生産を月次や週次といったサイクルで行っている場合、発注時期はそのサイクルに限定されてしまいます。
流通業者においても、 発注日または納品日を決めて運用しているところもあるでしょう。
そのような場合には、発注時期は制約条件として認め、その時々にいくつ発注すべきかを計算する定期不定量発注法を採用します。
LTV-Zaikoで在庫量の適正管理を!
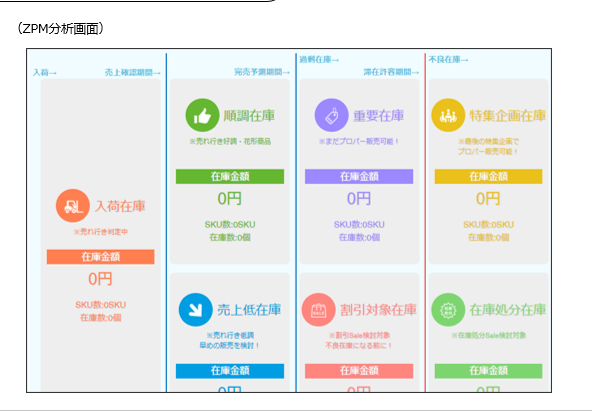
在庫管理の担当者の代わりを務めてくれるツール、それが「LTV-Zaiko」です。
LTV-Zaikoを使うことによって今ある在庫を販売開始日からの経過日数と消化率を計測し、独自に定めた7象限に自動的に振り分けます。
これにより商品の好調・不調を分かりやすく可視化することが可能で、自動計算された完売予測日をチェックすることで、欠品の早期発見・余剰在庫の削減に役立ちます。
SKU単位での商品登録設定もできるので、季節性の高い商品は早めの終売設定をしたり、定番商品は入荷ごとに閾値を設定し直したりできます。
まとめ
いかがでしたでしょうか。適切な在庫量に保つためには発注管理が一番の近道です。そのための方法として4つの発注法方を解説しました。業種や業態・状況に応じてベストな発注方法を採用してください。
ご参考になれば幸いです。
自ら余剰在庫を意識し、在庫消化を促進させる
ツールをお探しでは
ありませんか?
・定価で販売できる商品を値引きしていないか
・アナログ作業による在庫管理で業務負担が大きくなっていないか
・値引きやクーポンの判断が担当者の勘や慣例頼みになっていないか
企業のEC運用担当者が継続的に、より簡単に「余剰在庫の最小化」の工夫を行うことができ、CV(コンバージョン)や目先の短期的な売上、値引きの施策のみに頼らない粗利最大化の支援を行うことができます。さらにCRMシステム「LTV-Lab」との連携により売れない理由を究明し、アクションにつなげます。是非詳しい機能や特徴をサービスページからご覧ください。